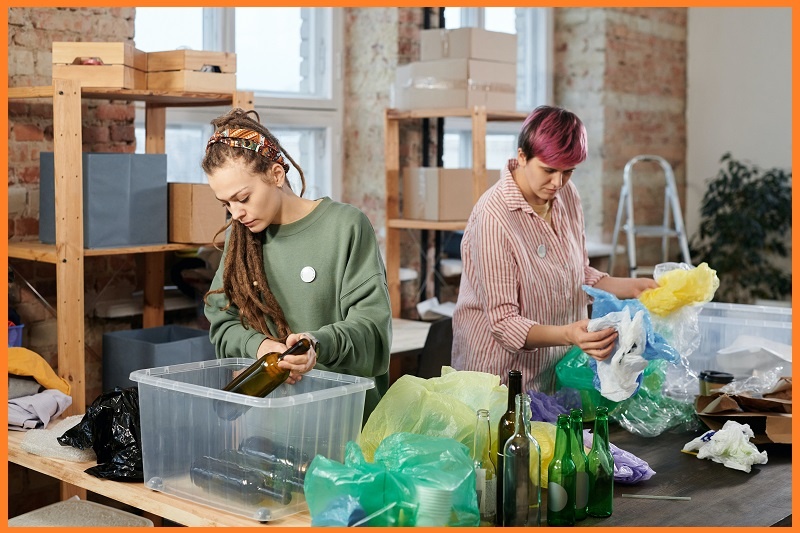
4 Ways To Reduce Your Business’s Inventory Waste
No business owner wants to deal with obsolete products, unused excesses, and products going to waste in their inventory and spending more money on restocking. Also, no business owner wants to deal with piling inventory expenses that constantly eat into business profits. If a major part of your business processes requires storing products, it’s important to learn how best to avoid inventory waste.
Whether you use the products or materials in your manufacturing process or sell them directly to customers, the following tips will help you reduce the chances of materials going to waste in your inventory.
- Optimize shelf life
One of the best ways to reduce waste and losses is to improve the shelf-life of all the products or materials stored. Whether in your business warehouse or any business storage solution, you want to ensure that your materials or products last as long as necessary.
A few things you can do to optimize shelf life include effective management, regular cleaning, and decluttering. You should also use only the best storage products that can directly affect the material shelf life. For example, if you run a mining or exploration business, you can take advantage of stackable core trays with one-piece molding and UV protection designed to prevent cross-contamination and reduce wastage. In other industries like food and agriculture, one way to optimize shelf life is to protect perishables from heat or light sources.
- Decide between first-in, first-out, and last-in, first-out
Even with systems in place to optimize shelf life, many types of inventory go to waste if you don’t use them soon enough. Even with products that tend to have better shelf-life, how much time they spend on the shelf still matters. That’s why you need to decide between what products come in first and get sold first and which ones come in last but go out first. Implementing a first-in, first-out (FIFO) and last-in, first-out (LIFO) rotation strategy allows you to evaluate what products or materials are sold, used, or disposed of first.
- Get a good inventory count
If you’re unsure what you have in your warehouse or how many items are stocked in your storeroom or store shelves, you risk things going bad without noticing. That’s because poor inventory count will most likely lead to storing products your customers do not need at the moment.
Doing a good inventory count allows you to set the right minimum inventory levels, ensuring that you always have products available when your customers need them, preventing waste in the process.
- Find ways to recover waste
Before you throw anything away, reconsider your options. Start by reassessing the waste.
- Is it possible to reuse it or put it back into the production process for a different purpose?
- Are there recycling solutions specially created for your kind of waste?
- Are there recycling companies you can sell your waste materials or products to?
Where it’s impossible to avoid waste, finding ways to recover the waste is crucial.