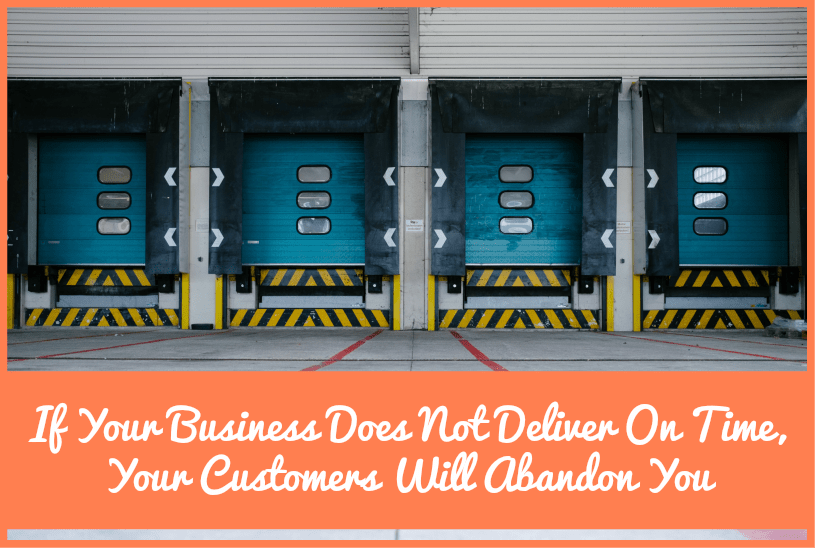
If Your Business Does Not Deliver On Time, Your Customers Will Abandon You
Businesses would like to believe that their customers will always be there for them through thick and thin. But people are surprisingly fickle, willing to jump ship at the first sign of trouble. It is a sobering realization for many bosses.
For eCommerce businesses – or any company that relies on logistics for that matter – failing to deliver on time brings substantial consequences.
Consumers are used to a world in which firms like Amazon deliver goods to their doors within a day or two. Sometimes they’ll branch out and try other vendors, but if they don’t deliver on time, they end up regretting their decision and just head straight back to Amazon.
As a company, therefore, you need to be taking steps right now to ensure that this doesn’t happen. You want your customers to stick with you for the long-term. In this post, we’re going to take a look at some of the strategies that you can use to make deliveries on time. Please read on to find out more.
Start Recording All Your Logistics Data
If there’s a problem with your supply chain or delivery process, you need to be able to pinpoint the issue. You don’t want to be in a position where you know there’s a problem because customers are complaining, but you have no idea what to do about it.
Break down your supply process and delivery into a series of steps that you can measure.
Look, for instance, at the amount of time it takes for goods to leave your warehouse after customers order, or how long it takes to get products from the port to your facility.
Keep track of all these measures over time so that you can identify problems that might be causing issues on the customer end.
Look For Weaknesses In Your Supply Chain
The reason you can’t deliver to customers on time might not have anything to do with your operations or those of your delivery partners. It could, instead, be an issue further up the supply chain with one of your suppliers.
Knowing whether you have a supply chain issue can be a challenge.
If you’re not a logistics expert, problems can sometimes be challenging to diagnose. Your supplier may be using the wrong type of transportation service, or they may have a poor business model.
If they’re shipping small volumes to you, then they may be waiting to fill up trucks before sending them to your facility. Little do they know that they could save money on LTL freight shipping if they went through the right channels. Sometimes, you’ll need to have a stern conversation with your supplier about their logistics utilization and recommend they change it.
Train Your Employees
Finally, it’s worth looking internally to see whether your employees are operating at maximum efficiency. If you have an issue with dwell time, then it suggests a problem with employees’ ability to know what to do next. Training can help reduce confusion, make product selection more efficient, and help to ensure timely deliveries.
© New To HR